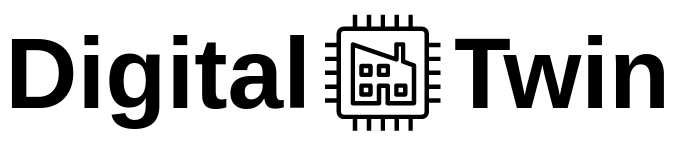
Today I would like to talk about the concept of a digital twin.
I will explain this term using few examples - from digital twin of a simple sensor to complete factory.
I will cover what is needed to provide business value from a digital twin and how to extend this concept.
Video
Sensor
A simple sensor can be described by its:
- metadata - for example:
- serial number
- vendor
- range of measured values
- readings (data it gathers from the environment).
Digital representation of metadata and readings can be described as a digital twin of that sensor.
To obtain a business value from digital twin, we need to process it. Before we can process it, we need to send this data to the cloud (or any backend system) and store it in database.
digital twin of a single sensor is not very useful but it shows the overall concept. Let’s move to another example.
Equipment
A piece of factory equipment can be described by its:
- metadata - for example:
- serial number
- vendor
- production settings - for example:
- type of currently manufactured part
- required pressure
- engine rotation speed
- readings from sensors attached to this equipment
We already covered metadata and readings; production settings are especially important.
Typically production settings are configured by a human (equipment operator).
Manual tasks are error-prone, so we are going to leverage digital twin and automate them.
The process looks as follows:
- Gather data related to this equipment and attached sensors.
- Send it to the backend system.
- Store historical data.
- Analyze historical data.
- Create production settings recommendation engine (it might use Machine Learning or some simpler solution)
- Send production settings recommendation (during the validation phase those settings should be reviewed by equipment operator; in production deployment equipment configuration is updated automatically)
To verify the recommendation engine we need to measure the impact of proposed settings on the quality of manufactured parts. This is usually done by dedicated sensors (for instance cameras taking pictures of parts and detecting defects).
The edge analytics is a very broad topic that I will cover another time. Today we are focusing on the concept of digital twin so let’s move to another example.
Production line
The same concepts I described for equipment can be applied to the digital twin of a production line.
digital twin of a production line includes:
- metadata information about the line itself
- production settings
- readings from sensors attached to the line
- digital twins of equipment on that production line
We added additional layer using the same concepts - let’s extend this example further.
Factory
digital twin of a factory extends production line. On this level we can include local applications or databases to create more accurate representation of a factory.
We created a virtual representation of equipment and sensors running in the factory. We can gather metadata and readings from every layer of our factory and store this data in the cloud.
Leveraging that data we can simulate factory equipment and try to predict the impact of potential production settings on the quality of manufactured parts.
Detecting anomalies in sensor readings can be used for a predictive maintenance of the equipment (so it can be serviced before it actually breaks).
Those are just a few examples how we can leverage the digital twin in the real life.
Summary
We started from a simple digital twin of a single sensor.
Created digital twin of complex equipment.
Analyzed production settings and readings from sensors to create the recommendation engine.
Provided business value - increased performance of monitored equipment and quality of manufactured parts.
Extended the concept of digital twin to create a virtual representation of a complete factory.
I hope that this presentation was interesting for you and showed how to leverage the concept of a digital twin.
